Reports and Statistics
Challenge! International Business: Kodai Sangyo Co., Ltd. - Environmentally friendly cypress products from Fukushima to the world
July 2014
If you visit this place, you will find yourself enveloped and relaxed in the pleasant scent of Japanese cypresses. Kodai Sangyo Co., Ltd., engaged in manufacturing and sales of the household wooden products, embarked on a challenge to disseminate the cypress cutting boards to the world under the mantra of "bringing the warmth and a touch of the color of wood into everyday life"

Sushi tray (FSC certification) with both sides processed (picture on the left), achieving a stylish design
Catalyst for the activity – Great East Japan Earthquake
Kodai Sangyo Co., Ltd. handles a comprehensive range of household wooden products. Since its foundation in 1972, the company has made efforts for modernization of equipment and implementation of an IT system in line with the needs of the times and has worked to develop new products and cultivate the new market. The company's major products include kitchen utensils, bathroom products, and self-assembly wooden racks. Major clients are large home-improvement stores, and it has engaged solely in domestic-trade.
However, the situation has dramatically changed since the Great East Japan Earthquake occurred in 2011. The company's head office in Motomiya is only 55 kilometers from the Fukushima No.1 Nuclear Power Plant. Fortunately all employees were safe but the factory suffered considerable damage, and commodity distribution was blocked, creating a situation where products could not be made for a while. Despite progress in recovery efforts, sales of the products in Western Japan declined sharply owing to harmful rumors, regardless of the company's own measurements of the radiation dosage executed every morning since the Fukushima accident never having exceeded the standard level.
In order to recover stagnant sales and protect employment, the company decided to develop the overseas market. To begin with, it ran a booth at the New York International Gift Fair held in January 2012. That's where the representative director received assurance that the cypress products were received well in overseas markets. The natural antibacterial properties of cypress and the softer surface of the cutting board which protects the sharpened edge of a knife became the big selling point. The performance of spraying water on the cypress wood shavings attracted many visitors to its booth who were allured by the comfortable aroma.
Since then, the company has continued to participate in various exhibitions. As for the above-mentioned New York International Gift Fair, the company made a presentation in August 2012 and January 2013 and participated in the Chicago Home & Housewares Show in 2013 and 2014. The range of products to be marketed overseas includes kitchen utensils and bathroom products, of which cypress products are the main products, with the cypress cutting boards being the company's leading products. The cutting boards come in many different shapes and sizes made from different materials, and the needs are different according to the country. In Japan, the most common shape for cutting boards is rectangular. However, in the U.S., there are diverse demands for cutting boards, each suitable for different tasks; round ones for serving pizzas, round ones with a handle and a big tray-size board for hors d'oeuvre cheese and hams. You have to imagine the case where the designs and the sizes of products fail to match the customers' needs owing to different cooking and eating habits. Fortunately, the company has a production system responding to individual needs and requirements regardless of how small the batch of orders, and believes it can offer an advantage over competing large-volume manufacturers overseas.
Wooden materials from the Hinoki cypress tree are familiar to Japanese. The cypress aroma balls are easily available. Not only do they serve as aromatic air freshener used on a daily basis, they also have a relaxing effect during bath time and at bedtime. However, the natural geographical distribution of cypress is limited to Japan (from Fukushima in the north to Yakushima Island in Kagoshima in the south) and Taiwan. Cypress isn't a well-known material for foreign people. As a matter of fact, these cypress products were faced with problems when they were first released overseas. They became cracked and warped when they were used abroad. The principal cause was the climate conditions being different from Japan. It turned out that the products suffered damage due to changes in moisture levels. To solve this problem, the company asked the Fukushima Technology Centre, a public test institute of the prefecture for its assistance. They developed a coating material that prevents cracks due to changes in moisture levels and succeeded in preventing further defects by applying the coating material on the cross-section surface of the shorter side of the board.
The FSC certification is the hallmark
Although the project to cultivate the overseas market was initiated by the Earthquake, there are other factors that have facilitated the overseas development.
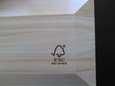
Since the 1990s, before the start of overseas development, the company has been implementing efforts to make effective use of timbers from forest thinning to make eco-friendly wooden products. In 2005, the company acquired a certification (see note) as proof of appropriate use of timbers which is harmless to the environment. This certification is only awarded to timbers that are produced in an environmentally responsible and economically sustainable manner, and bring benefits to local communities, and such timbers are allowed to bear the FSC (Forest Stewardship Council) certification logo. The consumers, by buying the products affixed with this FSC logo, can support the global forest preservation indirectly. We may not be able to see products that have acquired FSC certification in Japan yet. However, the certification has already been highly valued overseas, and in getting the overseas development underway, it has become an important sales point for the company's products.
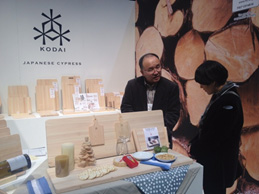
At the Chicago show, popular cutting board with a tray (picture on the right)
Preserving the hand-made process
In the beginning, in the U.S, due to deficiencies in the sales system, such as a failure to secure sufficient sales agents and warehouses, the company could only handle small orders. In particular, it was difficult to select a sales agent that could meet the needs of the company. Until the distributor agreement was concluded with the present sales agent, the company had to export products without signing an official distributor agreement, and problems arose at times because agreement could not be reached on contract details. However, through repeated visits to the U.S. and patient negotiations by the company representative director Masaaki Nemoto himself, eventually he managed to conclude a distributor agreement with a sales agent that met the needs of the company. Since then, the company has concluded a warehouse agreement and also increased the number of sales staff in Japan. Gradually, the company began handling larger volume orders and finally could supply the cypress cutting boards produced by OEM. The consignor was a kitchen knife manufacturer that the company met by coincidence at the Chicago show held in March 2013. This manufacturer set up a booth nearby and became interested in the cypress products, which led the manufacturer to place an order. Representatives from the kitchen knife company visited the company's booth many times during the four-day exhibition period. On the final day, the company's chief executive visited the booth to confirm the quality of the products and the direction of the business. After the exhibition, a representative came all the way to Fukushima to visit the manufacturing site and discuss the composition of the products. On his return, the Fukushima company exchanged emails with him and made numerous prototype products. Finally a written quotation was prepared at the end of 2013.
One year after the exhibition, in February 2014, a 20-ft transport container full of products was exported to the U.S. across the Pacific. The company continues to have lively discussions with the U.S. company to ensure increased supply of products by OEM and an increased product lineup for the future. According to business practices in Japan, products are normally delivered within two or three months after consultation with a client. However, in the case of the foreign clients, a diverse range of issues, including contract conclusion and prototype making had to be thoroughly discussed, and it took almost a year for the company to start delivering the products.
Actually, the cypress cutting boards have not been marketed domestically. The participation in the exhibition in Chicago led to an inquiry from the buyers from a Japanese firm, which then led to the decision to market the products that were intended for U.S. market in Japan this fall. Furthermore, in anticipation of deployment in the European market, the company is visiting the interior and design exhibition Maison et Objet in Paris and the consumer goods trade fare Ambiente in Frankfurt.
With an eye to future acquisition of new markets and dissemination of the company's cypress products in kitchens, living rooms and restaurants around the world, the company is continually striving to cultivate the overseas market.
Amane Kameda
JETRO Fukushima
Note: a certification system established by FSC (Forest Stewardship Council), an international non-profit organization which conducts activities in 80 countries throughout the world with a view to protecting forestry)
Kodai Sangyo Co., Ltd.
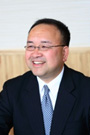
Foundation: May, 1972
Capital: 10 million yen
Annual sales: 580 million yen
Location: 68-1 Motomiya aza-Sakutadai, Motomiya-shi, Fukushima
Business description: manufacturing and sales of household wooden products
Number of employees: 41
Webpage: http://www.kodaimokuty.co.jp/