Rebuilding Japan
A seminar on "Japan's Automotive Industry, Achieving Recovery and Growth Through Monozukuri" held near Detroit
Friday, January 20, 2012
"The fundamental strength of Japanese manufacturing", demonstrated during the recovery from the March earthquake
JETRO Chicago's seminar, Japan's Automotive Industry, Achieving Recovery and Growth Through Monozukuri was held on December 8th in Novi, Michigan. The goal of the seminar was to facilitate the cooperation between Japan and the North American automotive parts industries.
Tatsuhiro Shindo, JETRO Chicago welcomed everyone by thanking attendees and speakers from the US and Japan for their efforts in the recovery. He also explained the reason this year's theme was chosen: the auto industry is a catalyst of the economy, the auto industry is critical to the Midwest United States and Japan, and also to show that monozukuri can be practiced outside of the factory floor environment. In his Opening Remarks, Kuninori Matsuda, Consul General of Japan in Detroit, opened the seminar's luncheon by thanking the US government, large corporations in Michigan, and the people of America for their immediate and un-fledging support in the recovery process. He pointed out that the US military was the first to respond, sending in 20,000 troops to help in the rescue and recovery efforts, the United States' largest such offshore effort in its history. The State of Michigan's, Douglas Smith, Michigan Economic Development Corporation, representing Governor Rick Snyder indicated that there are 50 Japanese companies in the city of Novi alone, and more than 500 in the State of Michigan, he stressed collaboration between companies.
During a special luncheon presentation, Neil De Koker, President and Chief Executive Officer of the Original Equipment Suppliers Association (OESA) reported on the current status of the devastated companies which he visited in Miyagi and Fukushima Prefectures at the end of November.
Mr. De Koker said "the speed of the recovery of damaged manufacturing sites and infrastructure was amazing. I was quite impressed to know that all companies did their utmost effort to maintain the continuity of the supply chain, such as requesting competitors to do alternative production. Each manufacturer has already finished their recovery activity and started to look to the future. I am sure this effort will be a driving force for future growth." He further reported that the speed of recovery, due to major automotive group companies helping any company in need of assistance, kept the loss of automobile production to a very low level of 100,000 units.
Mr. De Koker also reported that 93% of the automotive suppliers in the affected area were fully recovered, and 80% were at higher than pre-disaster production levels. He then recounted his visits to NOK and Alps Electric, two auto parts suppliers hit hard by the earthquake, but now fully functional. He cited examples of companies putting employees and their families first by making sure they were taken care of before production, and cited the fact that companies were running their competitors' tooling to help them out which provided everyone with a sense of how corporate competitiveness was put on the back burner, as everyone pulled together in the recovery effort.
Hidehiro Yokoo, President of JETRO, in the seminar's Opening Address said, "we would like to share with industry executives of the United States industry not only the damages of the Japanese manufacturing industry from The Great East Japan Earthquake, but also the recovery situation which was conducted in tremendous speed. Additionally, we would like to extend our gratitude to the United States for its kind understanding and support beginning from the assistance immediately after the earthquake occurred.In his talk on the seminar's objectives, Ted Kawashima, Director, Japan Auto Parts Industries Association (JAPIA) North America Office in Novi, Michigan, said that "from 2007 we held six seminars as a monozukuri seminar series to facilitate healthy competition and collaboration between Japan and the US automotive suppliers to create a sustainable supply base in the U.S. We would like to promote mutual understanding by sharing Japanese companies' ideas for monozukuri and business customs."
How the Monozukuri Ideal and Know-How were Importantly Utilized at the Earthquake Recovery Site
Nampachi Hayashi, Senior Technical Executive, Toyota Motor Corporation, Toyota City, Aichi, spoke for the first time in the United States to describe in detail about the tense situation and recovery activities at the earthquake reconstruction site. Mr. Hayashi led the cooperation activity for the re-start of production at the Naka plant of Renesas Electronics, which occupies a number one share of the global market in the automotive microcomputer market.
The reconstruction site of the Naka plant, was carried out not by the individual efforts of automakers, but by the united and horizontal cooperation from all of Japan's industries with the shared objective of helping the whole world's manufacturing.
Precisely, the following elements of monozukuri know-how were applied at the site; "Quick decision-making," "visualize the entire process and bottlenecks," "intensive communication (that) united individual members into a team," "making a whole strategy and clarifying priorities," were all fully utilized to shorten the term of reconstruction. As a result, Renesas was able to restart production after only a three month suspension which was six months ahead of schedule.
Mr. Hayashi said, "in order to deal with disaster recovery you have to have the ability to deal with new situations that are not included in any training manual. People can obtain this ability by doing their every day improvement activity, kaizen.
"It is also important that headquarters gives a mandate that support the activities and decisions being made by the people at the actual site." By making this clear, he pointed out that this type of ability from monozukuri* and Gemba* enables a quick recovery at the disaster site. He also said, "supply chain management which focuses not only on cost but also efficiency will be more important, such as local procurement and procurement diversification must be considered.
We should continue to utilize this type of heartfelt cooperation and horizontal collaboration of industries which was a positive result of the disaster, also we should continue our effort as a united Japan to achieve further recovery and future growth."
The Amazing Speed of Recovery Achieved by the Quick Decision of Leaders and the Close Communications of Employees
Nobuhiro Ozawa, Plant Manager of Nissan Motor Company Ltd's., Iwaki City plant explained about their earthquake recovery effort. Immediately after the earthquake they made a production re-start plan. Being supplied with human resources and life support supplies from other Nissan plants and from the whole of Japan they tried to re-start their production on the shortest schedule possible. They achieved recovery of their assembly line in only two months which was originally expected to take six months.
Nissan is working on a business continuity plan for future disasters based on this experience, such as establishing a production resumption standard to be made by every factory for use after a disaster.
Mr. Ozawa said, "at the emergency situation it is critically important to make a plan that will achieve recovery as quickly as possible," and also he emphasized the importance of making quick decisions. He added, "it is also important that the front line leader and leader at headquarters keep a close relationship. For the restart of production we needed many types of assistance from not only inside of the company but also outside of the company. This made me recognize the importance of human connections. "
Dave Thomas, Plant Manager, Keihin IPT Manufacturing LLC, introduced Keihin's damage from the earthquake as well as the recovery situation. He also explained about what his company in the United States did to support Keihin's plants in Japan that suffered during the earthquake.
Keihin's plants in Miyagi Prefecture and Tochigi Prefecture had damage to the die infrastructure, along with the die rack falling to the floor and suspension of electricity and water supply. While they worked very hard to resume production, they sent over one hundred employees to the suppliers which received larger damages, for the recovery of their supply chain. In the United States, Keihin raised donations through the company and American Red Cross. They also held charity car wash events to donate sales. In July, orders from customers were halved because of the shortage of parts supplies from Japan. But they did not conduct lay-offs. Instead, they utilized a voluntary vacation system to deal with the adjustment to lower production volumes.
After their production recovered to a normal level, they conducted employee re-training for those that have returned from voluntary vacations so that their employees could transition back to their original jobs.
Mr. Thomas said, "during the past four years, the automotive industry experienced so many head winds however, Keihin dealt with these damages and applied what we learned from these experiences. This helped us to keep damages to a minimum level during the flooding disaster in Thailand. I would like to think that the correspondent to the effect of the earthquake was a great training opportunity for our team. I would like to utilize this experience for the future."
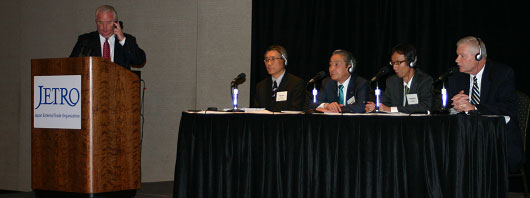
Local Staff's Monozukuri Spirit Enabled a Quick Recovery from a Tornado Disaster in Kentucky
Hiromi Ikehata, President of Toyoda Gosei North America Corporation made a presentation about the recovery activity from the tornado damage at the company's plant in Hopkinsville, Kentucky on April 4,, 2011.
This tornado which brought heavy damage in the United States was slightly reported in Japan because it occurred right after The Great East Japan Earthquake. However, at the Kentucky plant seven employees were injured by the direct touchdown of the tornado. Additionally, they had immense damage to their equipment for their silicon coating process. Immediately after the tornado passed they confirmed the safety and well-being of all their employees and shut off the main valve for gas and water supplies to prevent secondary damage. They also arranged for the use of a large generator which was introduced by a customer.
There were so many inquiries from customers that they opened a dedicated customer service hotline at Toyoda Gosei North American headquarters in Michigan to act as a channel to handle all inquiries from all customers, suppliers and related individuals. Additionally, there was a rumor among employees that the factory will be closed for an extended time. In order to prevent low morale they announced that the production will restart immediately.
Mr. Ikehata analyzed the factors which enabled the company to restart production within just one week with the full effort of the entire company. He emphasized that, "we trusted our local management staff to keep employees' morale positive, we got many forms of assistance from the local community and suppliers, and we maintained our infrastructure by ordering a large generator." Based on this experience he explained that it is necessary to establish a local network between local suppliers and facilities' companies. Additionally, he told of the importance of obtaining early and accurate information confirming a tornado alert. By listening to Mr. Ikehata's presentation participants were able to empathize with Toyoda Gosei's experience by recognizing that disaster in the form of a tornado is a familiar and critical risk issue for them.
They also understood that disaster will happen not only in Japan but also in the United States. Throughout his presentation the seminar room was remarkably quiet because of the full concentration of attendees.
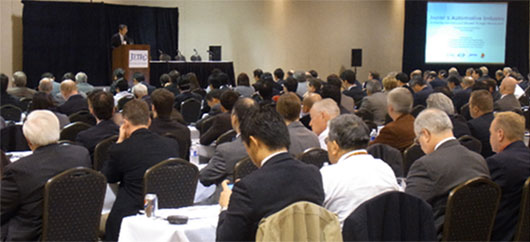
Will the Monozukuri Spirit Work Globally? Can the spirit of Monozukuri be extended in a global context outside of Japan?
These were points of discussion among our speakers during the seminar's question and answer session that was moderated by Glenn Stevens, Vice President, Sales and Marketing at OESA. Mr. Ikehata of Toyoda Gosei North America Corporation said, "Knowing the world of monozukuri is not enough to realize monozukuri. A basic principle in the philosophy of monozukuri is respecting a person and his and her well-being. If a company has this fundamental principle then its human resources will realize the spirit of monozukuri and it can be applied in a global context." Mr. N. Hayashi, Toyota Motor Corporation, also added, "we are already doing it (monozukuri) all over the world, if employees share the same objective and have appropriate leadership, the monozukuri spirit can be realized in every country."
* | Monozukuri ものづくりThe Japanese words mono (thing) and zukuri (process of making), when taken together, literally mean the process of making or creating things. However, the translation does not convey the accurate connotation of monozukuri. The concept is much more intense: monozukuri means having the spirit to produce excellent products and the ability to consistently improve production systems and processes. Suppliers hoping to develop closer collaboration with Japanese companies can benefit by embracing the mindset and practice of monozukuri at their respective companies. |
---|---|
* | Gemba 現場 Gemba means "actual place" or the place where real action occurs, that is where products or services are performed. In a manufacturing environment, the gemba is the shop floor, where all value is created. Genchi is similar meaning. |